Lithium-ion batteries are a key technology for e-mobility.
TECHNOLOGIES
HiQ-CARB aims to make technologies and processes for the production of highly conductive additives more environmentally friendly and uses, for example, bio-based materials and combines intelligently.
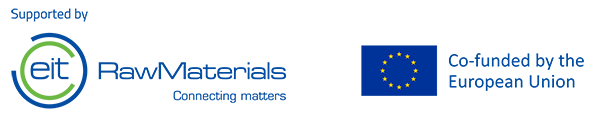
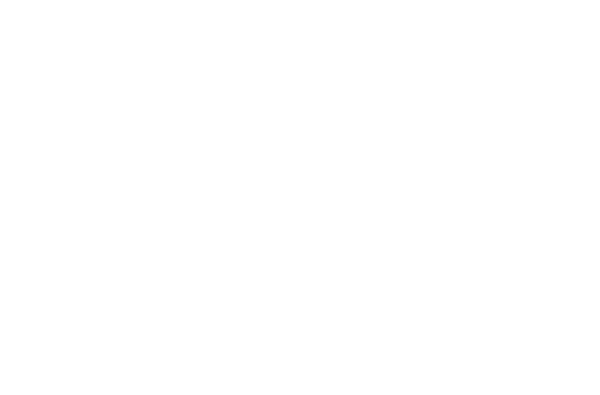
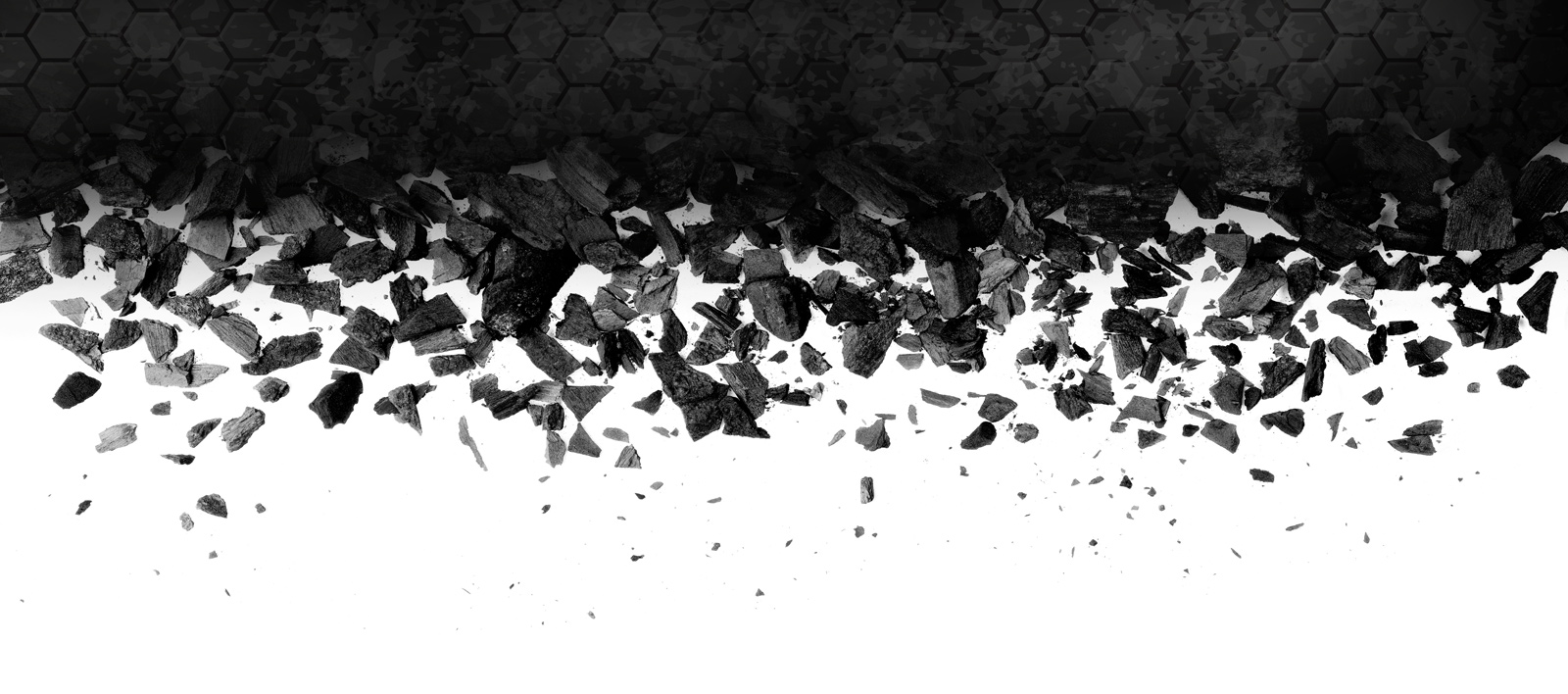
Improving the electronic conductivity of cathodes using sustainably produced carbons
Conductive additives, including conductive carbon black (CB), graphite powder, carbon nanotubes (CNTs), vapor grown carbon fibers (VGCF), graphene and porous carbons, are used in the production of lithium-ion batteries (LIBs). In an electrode, the additives form a conductive network between the active material particles (i.e. NMC, LMO, LFP, Graphite), which increases the conductivity, provides mechanical reinforcement and buffers volume changes within the electrode. Therefore, carbon plays a critical role in improving the electronic conductivity of electrodes. In HiQ-CARB, the important carbon additives for the cathodes of lithium-ion-batteries will be upscaled to produce more efficient and better performing battery cells based on European materials. These additives are the Acetylene Black of Orion Engineered Carbons and Carbon Nanotubes of Arkema, which in combination form an ideal conductive network within the battery electrode.
Carbon black is usually produced with high amounts of energy and process materials. HiQ-CARB will substitute standard conductive carbon black by new and much greener high-quality acetylene black manufactured by Orion Engineered Carbons. This contributes greatly to improved environmental performance, e. g. the reduction of the CO2 footprint of material production. In addition, the already commercialized standard carbon nanotubes will be replaced with much thinner carbon nanotubes by Arkema. This leads to less amounts of carbon materials for the same or even better battery performance and leads to an improved resource efficiency. In addition, this is the only nanotube material worldwide produced from a renewable bioethanol feedstock.
The challenge ahead is to tune the carbon properties in conjunction with the electrode design to maximize the cells’ power density without negative impact on the volumetric and gravimetric energy density by introducing superfluous amounts of carbon into the electrodes. This requirement offers business opportunities for EU chemical companies to meet the demand in the exponentially growing market by providing specially designed materials for high power or high energy density applications to cell manufacturers. The value chain for advanced European materials will be further developed.
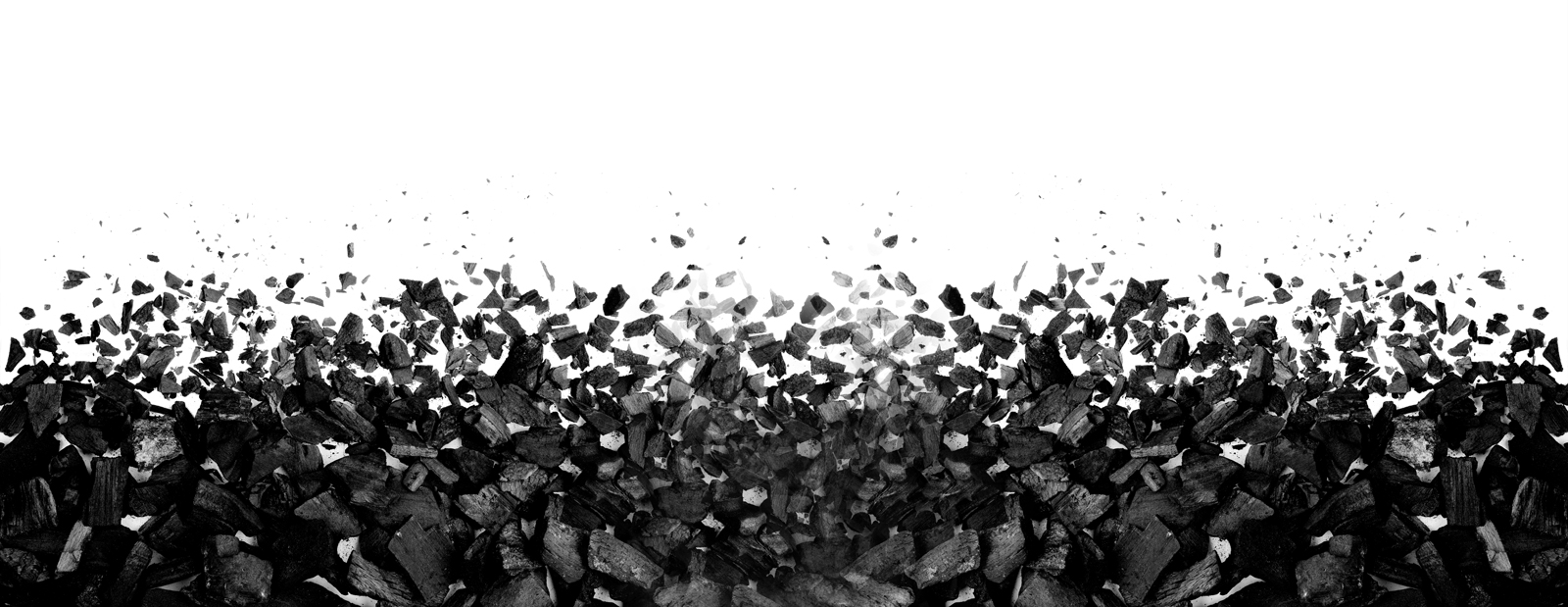